Mig Tig Wire Feed Aluminum Spooler
Many perceive MIG welding aluminum as complicated. But this is false and depends significantly on how you prepare the aluminum and set up your welding equipment. When you fail to prepare adequately, that's when you end up with poor results.
The MIG welding process is less complex and fussy than TIG welding aluminum. But the final weld joint quality is similar if you know the correct procedures.
So, in this article, you'll learn how to prepare this common metal, why aluminum is challenging to weld, what shielding gas to use, how to set up your MIG welder, and the proper welding technique.
Why is MIG Welding Aluminum Difficult?
Aluminum forms an oxide layer on its surface with a melting point much higher than aluminum. So, this oxide makes welding difficult.
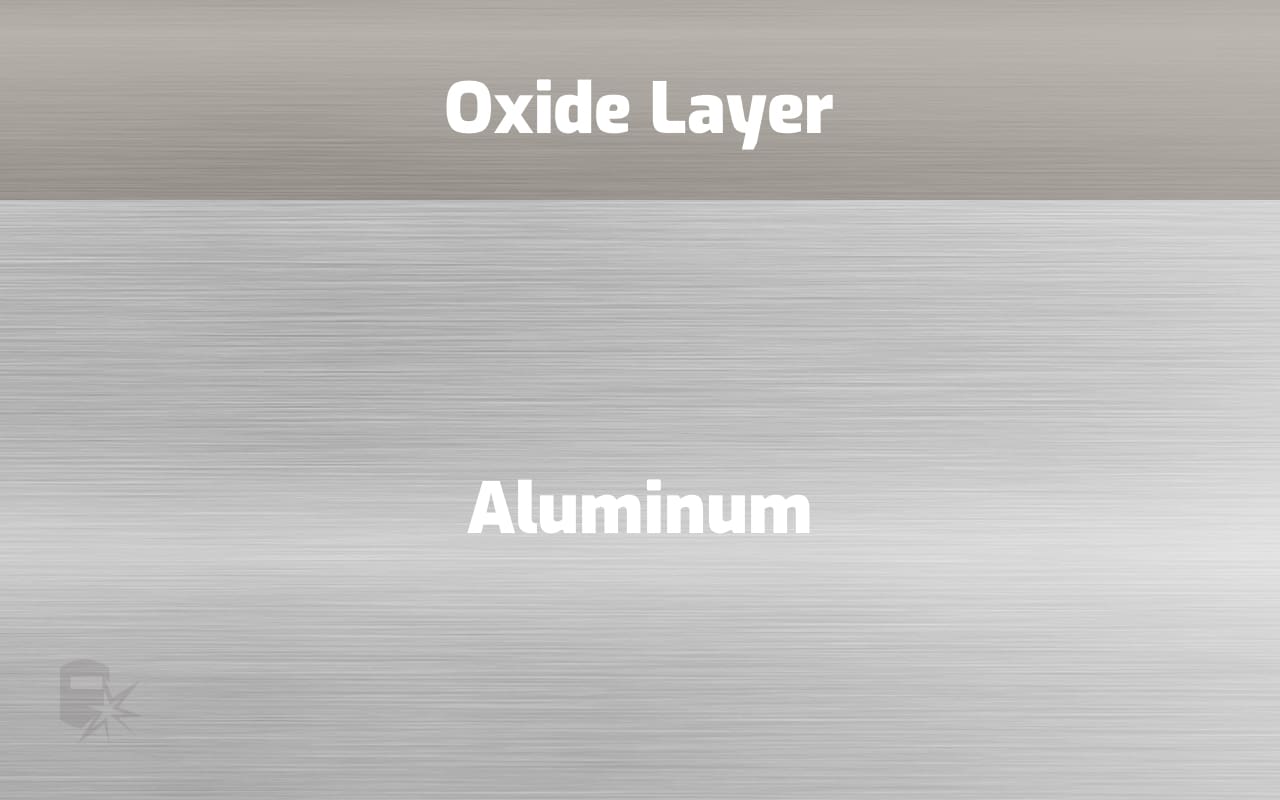
But, other aluminum properties like high heat conductivity, proclivity to cracking, and a high thermal expansion rate make aluminum notoriously tricky to weld.
So, let's discuss these issues separately in detail to help you avoid the most common pitfalls.
Related read : What is Gas Metal Arc Welding?
Surface Preparation
Aluminum oxide forms almost immediately when aluminum is exposed to air, preventing corrosion of the metal underneath. So, this surface layer is the key to aluminum's durability.
However, this protective layer melts at a 3700°F (2037°C) while the pure aluminum underneath melts at 1200°F (650°C). That's a huge difference.
If you want to weld aluminum, you must remove the oxide layer, or you'll melt the base aluminum and trap the oxide in the joint. The unmelted oxide inclusions cause a lack of fusion and reduce the joint's strength.
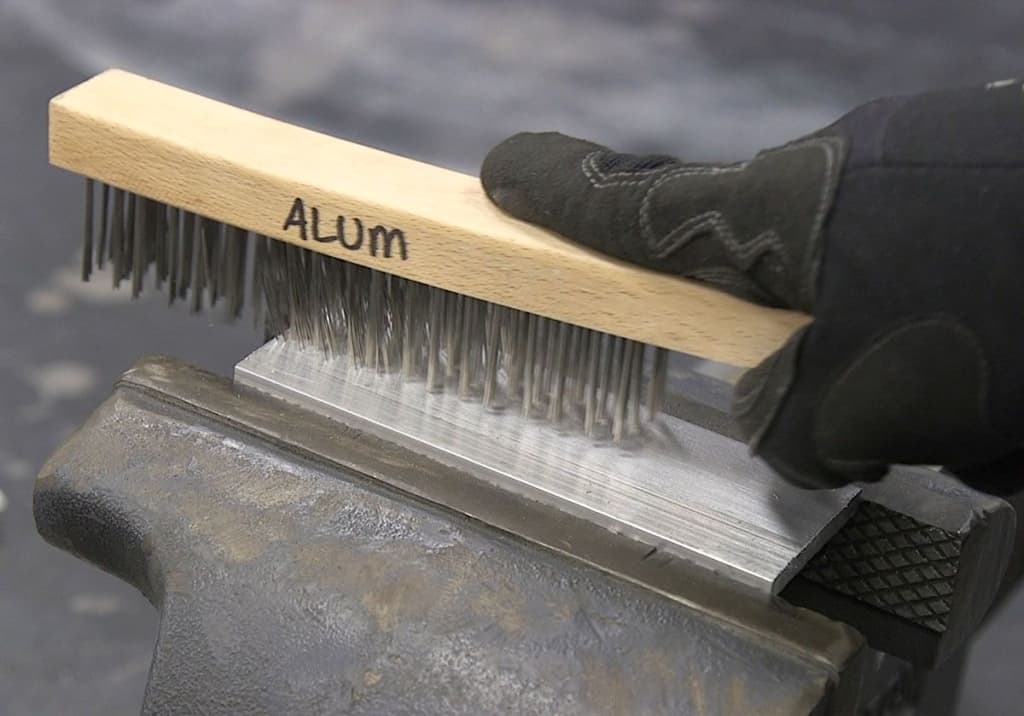
The most straightforward way to remove the aluminum oxide from the metal surface is using a stainless steel brush. However, before using the brush, you must first clean the surface of all dust, paint, oil, grease, and other contaminants. So, use a lint-free cloth to remove dust and oil and chemical solutions to remove grease and paint.
Otherwise, you'll embed the impurities into the brush scratches because aluminum is soft. Embedded particles burn during the welding process, and the resulting gases cause porosity.
Also, don't use a regular carbon steel wire to clean aluminum because it will contaminate it. Instead, use a stainless steel brush dedicated to working with aluminum. To prevent cross-contamination from carbon steel, label your tools that come in contact with the metal, especially abrasives, for aluminum-only.
High Heat Conductivity
Aluminum conducts heat five times faster than steel and expands as much as 6% when heated. Additionally, aluminum melts at much lower temperatures than steel. So, you must weld quickly to avoid burning through on thinner gauges.
Also, your weld heat rapidly moves away from the joint into the surrounding metal, thanks to aluminum's high heat conductivity. The only way to combat this issue is to crank up the amperage and voltage to apply more heat. But, since aluminum melts at low temperatures, you must move fast.
The trick is to find the sweet spot with the applied heat for the aluminum thickness you're welding. Additionally, preheating the part up to 200°F helps initiate the weld puddle without going crazy high with the amps, lowering the risk of burning through the material.
You must also take the expansion and the subsequent contraction into account. Otherwise, the internal stresses will cause cracks. Post-welding shrinkage of 6% is no joke. That's 6 cm for every 1 meter of joint length. So, create allowances in the joint and keep the welding length to a minimum.
Many Aluminum Alloys
There are over six hundred aluminum alloys, and most can be fusion welded. The 5xxx series of aluminum has excellent weldability. But high-strength aluminum alloys like the 2xxx series and 7010 or 7050 are tough to fusion weld.
Aluminum alloys are grouped according to their principal alloying element. Wrought aluminum is most commonly used, and it's designated using a four-digit system (XXXX).
- The first digit (i.e., 1xxx) indicates the principal alloying element
- The second digit (i.e., x2xx) represents the modification of the specific alloy within the series
- The third and fourth digits (i.e., xx50) identify the alloy within the principal series
For a general MIG welding guide, it's enough to understand how to read the principal alloying element (i.e., the first digit in the number) as shown in the table below. But, each alloy has unique properties to consider when welding.
Aluminum Series | Principal alloying element |
---|---|
1xxx | 99% Pure aluminum |
2xxx | Copper |
3xxx | Manganese |
4xxx | Silicon |
5xxx | Magnesium |
6xxx | Magnesium and Silicon |
7xxx | Zinc |
You will most likely weld 3000, 4000, 5000, or 6000 aluminum series using a 4043 or 5356 filler metal.
The ER4043 MIG wire is used to weld 2014, 3003, 3004, 4043, 5052, 6061, 6062, and 6063 aluminum alloys. It's the "general purpose" aluminum filler metal. You are unlikely to go wrong if you choose this wire. The 4043 alloy is resistant to cracking, and welds are highly ductile, which helps with aluminum shrinkage.
The ER5356 wire has a higher tensile strength than the ER4043 MIG wire. However, it's more prone to cracking. The ER5356 is used to weld 5050, 5052, 5056, 5083, 5086, 5154, 5356, 5454, and 5456 aluminum alloys.
Soft Aluminum Wire is Hard to Feed
MIG wire feed systems designed for steel wire often cannot handle aluminum wire because it is too soft. As a result, aluminum wire can get tangled up and create a "bird's nest" inside the feeder.
The MIG gun liner made for steel wire is also made from steel. This causes two problems for welding aluminum:
- The aluminum wire will probably kink in the liner.
- The liner can transfer steel particles into the weld pool because the aluminum wire rubs against it throughout the liner length.
Both problems are solved by using a graphene liner (carbon PTFE). However, there is still a slight chance of the wire getting tangled, depending on the gun's lead length and how straight you keep the lead from the wire feeder to the MIG gun.
So, if you want to maximize the wire feed's reliability, you should use a spool gun. These guns have miniature built-in wire feeding systems that accept a small spool of aluminum wire.
Since the wire's travel distance is so short, it's negligible, and there are no wire feeding issues. But, spool guns are bulky, heavy, and only accept small 1-2 lb wire spools.
If you use a graphene liner instead of the spool gun, keep the MIG lead straight, and you are unlikely to have issues. Additionally, use the ER5356 wire if possible because it's less likely to get kinked in the liner.
You can also use specialized push-pull guns with a second motorized wire feeder that works harmoniously with the MIG wire feeder. The push-pull gun pulls the wire as the wire feeder inside the welder pushes it through the lead liner. These systems are more expensive and are usually used in professional welding shops.
Shielding Gas Selection
Let's start by addressing the common mistake beginners make — you cannot use the 75/25 Ar/CO 2 shielding gas to weld aluminum.
MIG welding aluminum requires a 100% argon shielding gas or an argon-helium mixture. Carbon dioxide cannot be present in the shielding gas because this is a reactive gas. So, even a tiny amount of carbon dioxide will devastate the aluminum and create a severely impaired joint.
Straight argon is typically used, and it's the least expensive choice. However, if welding a thick piece of aluminum, adding helium to the mix increases the heat input and depth of penetration.
So, if your welding machine lacks power, you can improve penetration by adding helium. The more helium you add, the deeper the penetration. However, helium is expensive and reduces arc quality.
You can read all about shielding gases used for MIG welding in our separate article. But, you should stick with 100% argon for most aluminum welding jobs.
Welding Technique
The welding technique boils down to travel speed, torch angle, wire tip to work distance, and the MIG gun manipulation.
So, let's discuss each to help you successfully MIG weld aluminum.
Travel Speed
Since aluminum conducts heat rapidly, and the base aluminum melts at a relatively low temperature, you need to weld quickly. Unlike TIG welding aluminum, which lets you take your time, MIG welding requires you to make the weld without delay. Prepare yourself, position the gun, and once the arc goes off, move fast until you reach the end of the joint.
The base metal will get heated as you weld if the joint line is long. This requires you to increase welding speed even more. You'll burn through the metal if you use a uniform welding speed throughout the joint's length, especially if welding thin aluminum.
It takes some practice to increase the travel speed as you weld correctly. So, don't be discouraged if you fail at first.
Torch Angle And Travel Direction
You should always use a push (forehand) travel direction with a 10-25 degrees angle to MIG weld aluminum. If you try to pull the MIG gun, the shielding gas won't provide sufficient coverage, and the welds will develop porosity.
Related: Should you push or pull when MIG welding?
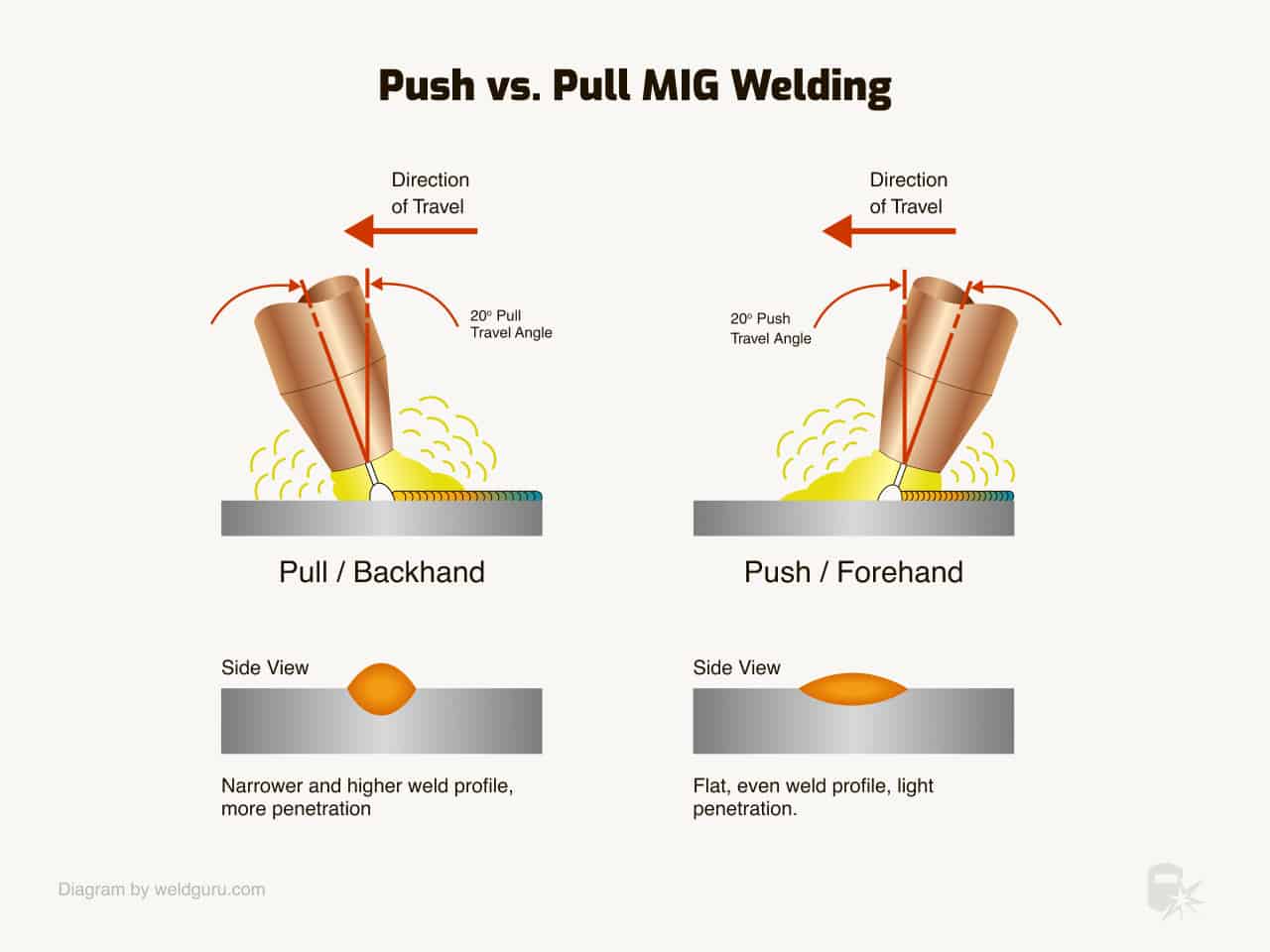
It's possible to drag the gun with the tip pointed in the opposite direction of pushing, but dragging risks dirty, porous welds.
Additionally, MIG welding aluminum requires a stringer bead. So, don't weave the MIG gun because this reduces the penetration and fusion quality.
Tip to Work Distance
A correct tip-to-work distance is about 3/4-inch. So, the MIG torch tip and workpiece gap is about 1/4-inch larger than when welding steel.
Additionally, if possible, you should keep the contact tip recessed inside the nozzle about 1/8 inch. Otherwise, you risk the wire burning back to the contact tip because of high reflective heat from the weld pool.
Spray Instead of Short Circuit Transfer
It's necessary to use a spray transfer to successfully MIG weld aluminum, not the short circuit transfer used for welding steel.
The short circuit transfer establishes the arc when the wire touches the metal. Then, as the wire burns back, molten filler metal drops into the weld pool, and the arc is extinguished. The process initiates again when the wire feeder pushes some more wire into the metal. This happens many times per second, and you can even see how the arc is established and goes out with the naked eye.
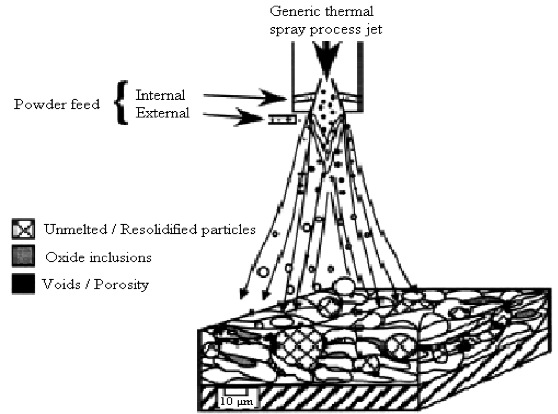
With spray transfer mode, the arc doesn't go out until you release the trigger on the MIG gun. Once the wire touches the metal, the arc initiates and remains constant. The wire doesn't melt into big blobs of metal but deposits filler wire in tiny droplets sprayed into the weld pool.
To achieve spray transfer when MIG welding, you must simultaneously increase the wire feeding speed and voltage to settings higher than those used for short circuit transfer. The minimum voltage required for spray transfer is 20-24V, depending on the welded part thickness and the welding machine.
The spray transfer mode inputs more heat into the material, creates a highly liquid weld pool, reduces spatter, and allows high travel speeds. While it sounds good in theory, spray transfer requires more skill because it's easy to warp the material or burn through it due to the high heat input.
How To Set Your MIG Welder Settings Right for Aluminum
We mentioned the necessary voltage for spray transfer above, but there are many other settings you need to set correctly to MIG weld aluminum.
So, let's go through each MIG welder setting and discuss the shielding gas flow rate to help you avoid common issues.
1. Attaching a Spool or Push-pull Gun
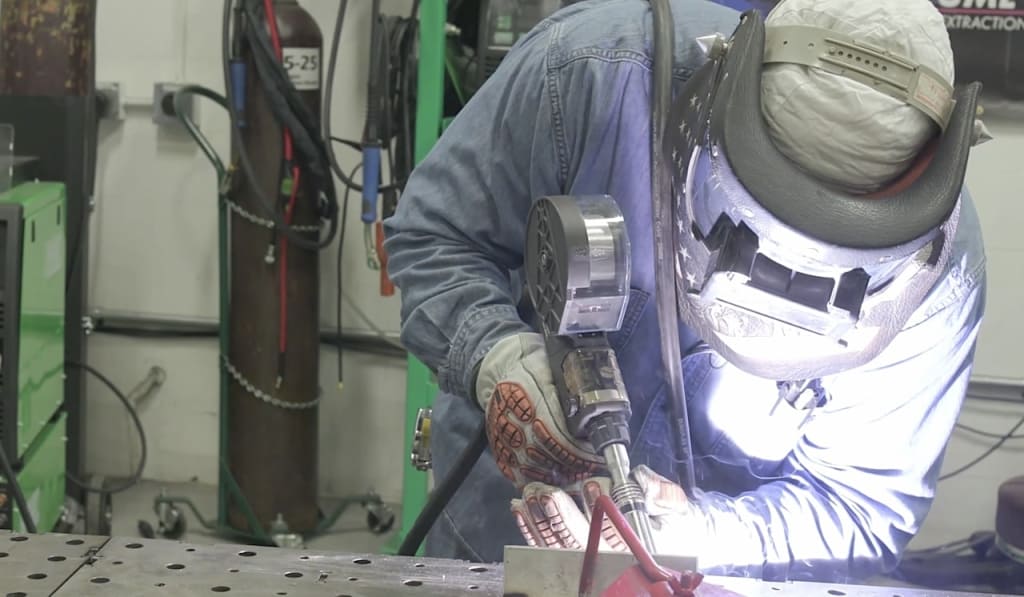
Not every MIG welder supports a spool gun or push-pull connection. Additionally, these torches are not universal. Every brand makes its own spool guns and push-pull systems for its MIG welder models.
If you are unsure if your welder supports a spool gun or a push-pull gun, check the manufacturer's website. If you already own a MIG welder with a gun for welding aluminum, follow the manufacturer's instructions on how to attach everything.
While not universal, most spool or push-pull guns replace the regular MIG torch lead. Additionally, a power cable for a spool gun is often necessary to attach somewhere on the front panel of the welding machine.
But, there are no hard rules here because some manufacturers provide power to the spool gun through the welding lead that supplies the shielding gas.
2. Wire Feed Settings
Wire feed speeds for MIG welding aluminum need to be significantly higher compared to welding mild steel. Most welding machine manufacturers provide a MIG settings chart. Check the user manual if your machine doesn't include the chart on the inside compartment.
But, if your MIG welder doesn't have a settings chart, a good rule of thumb is to increase the wire feed speed used for mild steel by about 30-100%.
Below is a sample chart offered with the Eastwood MIG 250 welder. Your machine may require a slightly different setup, but settings shouldn't deviate much.
3. Set the Polarity
MIG welding aluminum requires direct current electrode positive ("DCEP") polarity, just like welding steel. The only reason to switch your MIG welder to DCEN is for the flux-cored welding process.
4. Choosing the Amperage Output
Amperage output is determined by the wire feed speed when MIG welding. The higher the speed, the more amperage needed to the weld metal and the deeper the penetration.
The exact amperage output for a given wire feed speed depends on the welder brand. So, one machine may output 200A using a 400 IPM wire feeding speed, while another may output 180A at the same speed.
Additionally, the wire diameter also influences the output amperage. The thicker the wire, the lower the amperage output. So, a thicker wire requires a higher wire feeding speed to output the same amperage than a thinner wire.
Some welding machines like ESAB Rebel 205ic show the exact amperage on display as you weld. That way, you'll get visual confirmation of how much amperage is provided with the set wire feed speed.
5. Shielding Gas Flow Rate
Since MIG welding aluminum requires moving the torch quickly, you need a high shielding gas flow rate. While you may achieve reliable welds with 15 cubic feet per hour ("CFH") to weld carbon steel, MIG welding aluminum requires a minimum of 20 CFH when using straight argon. But, if you notice porosity in your welds, increase the flow to about 30 CFH.
However, if you use argon and helium mixtures, you'll need an even higher shielding gas flow rate. Helium is much lighter than air and argon, so you may need up to a 50 CFH flow rate depending on the helium percentage in the mixture.
Summary for a "Typical" Aluminum MIG Weld
We made the table below to condense everything in this article and provide a quick reference guide.
You can use the chart to make typical, basic aluminum MIG weld, but remember that specialized alloys, thick aluminum parts, complex joint geometries, and out-of-position welding may require a more nuanced approach.
Wrapping It
Aluminum is a complex material to weld, and using the MIG welding process whenever possible is preferred to TIG welding because it's easier. Still, if you've never welded aluminum before, you may think that the entire process is too complex.
But, there are significantly fewer variables to consider when MIG welding aluminum (compared to TIG welding). So, MIG welding is a good way for a beginner to dip their toes into welding this popular material.
MIG welding of aluminum is not as hard as some perceive it. With the know-how presented in this article, MIG welding allows you to tackle this common metal.
The key areas to focus on are aluminum precleaning, tuning in your MIG welder settings, and mastering your welding technique. You'll get the hang of it with some practice. Remember to make test welds on a scrap piece before welding something valuable.
Related Reads
TIG Welding Aluminum
Stick Welding Aluminum
Source: https://weldguru.com/mig-welding-aluminum/
Posting Komentar untuk "Mig Tig Wire Feed Aluminum Spooler"